化学沉镍金(ENEIG)工艺作为无铅适应性的一种表面处理已经成为无铅电子产品表面处理的主流工艺,化学沉镍金表面处理的镀层质量、表面清洁程度和镍腐蚀现象等是影响其可焊性的重要因素。本文结合具体的失效案例,详细介绍了由上述原因导致PCB焊盘可焊性不良的表现形式、分析方法和思路,可为PCB业界同行在分析可焊性不良问题时提供参考。
随着无铅工业时代的到来,常见的PCB表面处理方式有:化镍金(ENIG)、沉银(Immersion Silver)、沉锡(Immersion Tin)和OSP膜(Organic Solderability Preservative)[1-2]。其中,沉金也叫无电镍金、沉镍浸金或化金,是一种在印制线路板(PCB)裸铜表面涂覆可焊性涂层的工艺,其集焊接、接触导通、打线和散热等功能于一身,满足了日益复杂的PCB组装焊接要求,受到PCBA(printed circuit boardassembly,即PCB组装)客户的亲睐[3]。
但随着无铅焊接峰值温度的提高,因无铅焊料的熔点为217℃,使焊接工艺窗口由50 ℃(有铅焊接)减小到15 ℃(无铅焊接)。焊料、PCB表面处理和元器件表面处理的多元化,出现了很多兼容性问题,尤其是带来了更复杂的沉金PCB可焊性问题[4]。本文将重点分享几例常见沉金PCB可焊性不良的失效案例,总结其失效机理和失效原因,为分析、解决沉金PCB可焊性不良问题提供有力的分析方法和思路。
一般而言,化学沉镍金工艺中的金层厚度要求控制在0.05 ~0.15μm之间,金层偏薄将使其对镍层的保护作用会有所下降,尤其是导致经过长时间的储存、贴装前烘烤或者贴装过程中的高温老化后其引起的PCB可焊性不良现象会更加显著。以下分享一例由金厚偏薄引起的焊接不良的案例,不良外观如下图1所示:
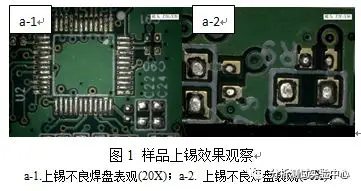
由以上图片可知,不良PCB焊盘上锡不良而且呈现金面发白现象。
使用X-Ray测厚仪对PCB进行金厚测量确认,结果如表1所示:

如表1所示,使用X-ray测厚仪对PCBA未焊接位置金厚进行测试,发现不良PCB焊盘的平均金厚0.033μm,金厚低于工艺控制要求。
通过扫描电子显微镜及X射线能谱仪上锡不良的焊盘进行表面形貌观察(SEM)及元素分析(EDS),确认焊接不良位置的表面情况,结果如下图2所示:
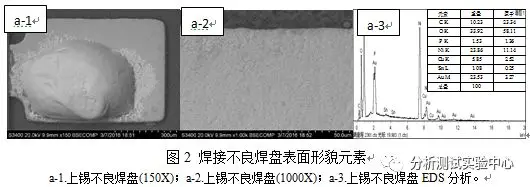
由以上SEM图片和EDS分析结果得知,上锡不良焊盘未发现明显污染物,说明该位置可焊性不良非污染导致;而EDS元素分析发现焊盘表面的O(氧)含量偏高,这是由于金厚偏薄,焊接时高温作用使焊盘中的镍原子迁移至金层表面,并在焊盘表面生成了氧化镍。
为改善因现有板金层过薄导致镍原子在焊盘表面被氧化而造成可焊性不良的问题,对上锡不良的焊盘进行酸洗后浸锡,结果如图3所示。发现酸洗后原先上锡不良的位置上锡良好。酸洗能够有效去除板面的氧化层,说明原先金层对镍层的保护不足,导致在回流焊接过程中镍原子迁移至金层表面被氧化,生成的含镍氧化物熔点甚至高达2000℃,在回流焊接过程中阻挡焊接基底与锡料原子之间的相互扩散,从而使焊盘的润湿性能下降,导致上锡不良。
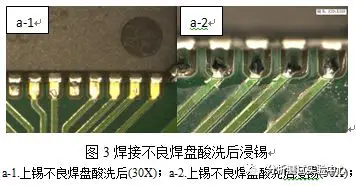
2.2.1 金面杂质离子残留
在沉金表面处理后,如焊盘表面未清洗干净,会有氯、溴等卤素离子或其他酸碱性杂质离子残留。这些残留物与空气中的氧和水汽在长时间的作用下就会使镀层氧化,从而降低焊盘的可焊性。即使PCB清洗干净,而由于存放环境不良,长时间存放在潮湿空气或者含有酸、碱等物质的气氛中,焊盘表面也会逐渐发生氧化而出现表面异色等现象,形成可焊性不良的失效现象。以下分享一例PCB焊盘表面被氧化物污染导致上锡不良的案例,不良板的外观如下图4所示:
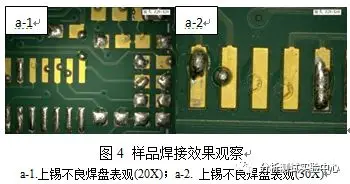
由以上图片可知,不良PCB焊盘不润湿,出现“金不溶”现象。
对PCBA未焊接但金面存在异色发红的位置进行形貌观察及元素分析,分析确认其可焊性不良的原因,结果如下图5所示:
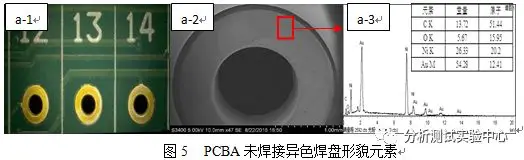
PCBA部分焊盘存在发红现象,EDS元素分析发红位置C(碳)含量偏高,未发现其它异常特征元素,疑似存在污染离子。
为验证其可焊性不良的真正原因,对金面发红的焊盘进行酸洗前后的可焊性验证,浸锡结果表明,金面发红的焊盘均出现可焊性不良现象,而酸洗后原先上锡不良的位置上锡良好。酸洗能够有效去除板面的氧化层,说明该板不良主要是由于焊盘表面存在一层较薄的氧化物,而经过稀盐酸清洗能将其去除,从而改善焊盘的润湿效果。
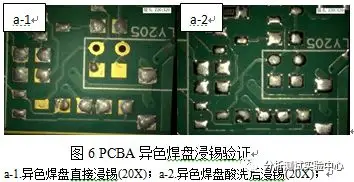
2.2.2 金面异物残留
表面污染除了氧化物以为,还有其他的污染也会导致PCB出现可焊性不良现象。以下分享一例PCB焊盘阻焊余胶导致上锡不良的案例,不良外观如下图7所示:
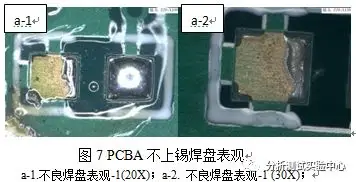
由以上图片可知,焊接不良焊盘表面分布着大量的绿色污染物,从焊接效果可知,上锡不良焊盘的失效模式为不润湿模式,即锡膏不润湿焊盘,怀疑该焊盘不上锡原因可能是焊盘表面为阻焊余胶。
通过扫描电子显微镜及X射线能谱仪对不上锡的焊盘表面及正常钻位置进行微观形貌观察及元素分析,结果如下图8所示:
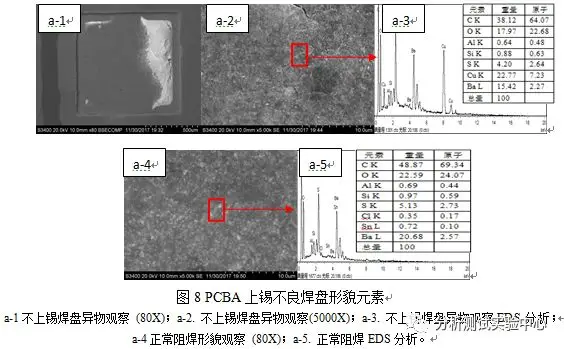
微观形貌观察发现,在成份像背散射模式下,焊盘表面污染物与周边阻焊存在相似性,其二次像形貌与阻焊形貌也存在一致性,EDS元素分析表明,该污染物与阻焊均含有元素Si、S、Ba一致,故进一步推断污染物为阻焊余胶。
从上述分析看出,造成该板可焊性不良的原因为金面残留有阻焊余胶。为了进一步验证导致不良板可焊性不良的根本原因,使用氢氧化钠溶液,在水浴锅中80℃恒温半小时,去除阻焊余胶后,分析焊盘形貌元素,如图9所示。
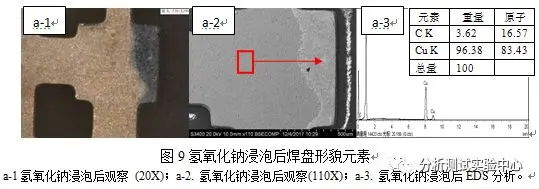
由以上形貌元素分析得,褪阻焊后的焊盘表面为铜面,没有Ni(镍)和Au(金)元素。
对褪阻焊后的焊盘进行可焊性验证测试,结果表面不上锡焊盘表面残留的阻焊褪掉后浸锡可焊性良好,说明该板不上锡主要原因为焊盘表面阻焊余胶导致该焊盘未沉上镍金,在焊接过程中阻挡了焊料在焊盘表面的扩散从而引起可焊性不良现象。
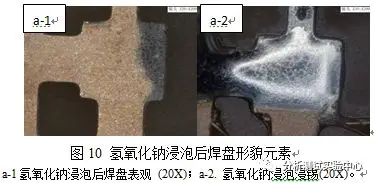
镍层作为金层和铜层之间的过渡层,起到阻挡铜和金相互扩散的作用,同时其还是焊接的基底层。镍层过薄会削弱其阻挡铜金原子之间的扩散作用,同时导致有效焊接的厚度变薄,无法形成良好的焊点。对于化学镀镍金工艺来说,其本质是一个置换反应,由于置换反应获得的金层为疏松多孔结构,且金原子体积大,在浸金反应后期,虽然金层厚度不再增加,但金原子间隙下的镍层仍然可以继续被置换。镍过度置换产生的镍离子往往积累在金层下面,镍离子被氧化后就生成黑色氧化物,这也就是所谓的黑盘(镍腐蚀)。镍氧化物的浸润能力很差,因而黑盘对镍金层的可焊性会产生致命影响。以下分享一例焊接后部分焊盘发黑不良的案例,不良外观图片如下图11所示:
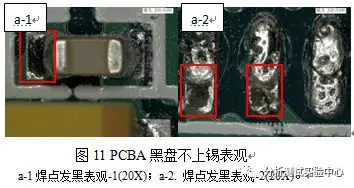
通过扫描电子显微镜及X射线能谱仪对上锡不良焊盘进行微观形貌观察及元素分析,结果如图12所示:
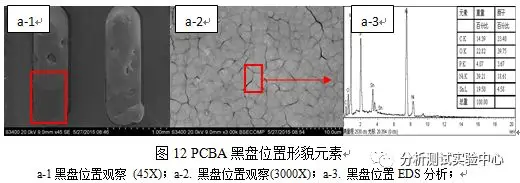
通过以上分析发现,发黑焊点表面主要元素为C(碳)、O(氧)、P(磷)、Ni(镍)、Sn(锡),且镍层晶格之间呈现“龟裂状”,疑似有镍腐蚀现象。一般焊接过程应为:首先Au(金)在高温下扩散至焊点内部,然后Ni(镍)和Sn(锡)之间形成IMC层。焊点发黑处未发现Au(金),说明第一步已经完成;但是第二步却未完成,焊点发黑处均为裸露的Ni(镍)层晶格形态。而镍在高温下急剧氧化使得焊点呈现黑色,因此O(氧)含量偏高。
以上分析发现黑盘位置存在表面镍腐蚀现象,现对该焊点及未焊接的孔环微切片制作后再观察其截面镍层情况,结果如下图13所示:
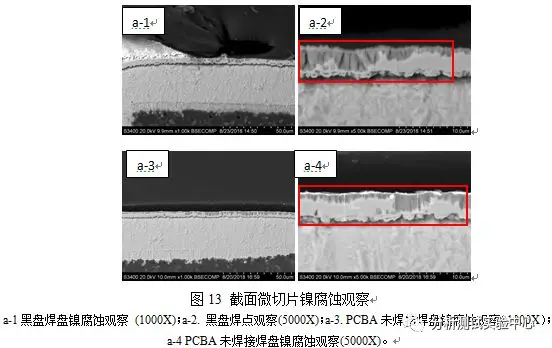
通过黑盘焊点截面观察发现,镍层存在严重的连续性镍腐蚀现象;未焊接焊盘的截面镍腐蚀观察,同样发现深度镍腐蚀现象,金层以下镍层已完全氧化、钝化,在扫描电子显微镜背散射像(BSE)下呈现黑色形态(连续性镍腐蚀)。由此说明该板焊接后出现黑盘现象主要是严重镍腐蚀所引起。
金层作为最外层的保护层,起到抗腐蚀防氧化的作用。金层表面有划伤、孔洞及经过喷砂处理均会造成对镍层的保护不足;镍层作为金层和铜层之间的过渡层,起到阻挡铜和金相互扩散的作用,同时其还是焊接的基底层,若镍层出现孔洞或者疏松等现象均会引起镍层氧化不上锡现象。
2.4.1 金面孔洞
以下分享一例金面孔洞导致可焊性不良的案例。不良外观如下图14所示:
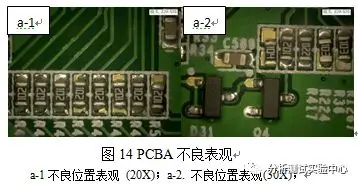
通过扫描电子显微镜及X射线能谱仪对上锡不良焊盘进行微观形貌观察及元素分析,结果如图15所示:
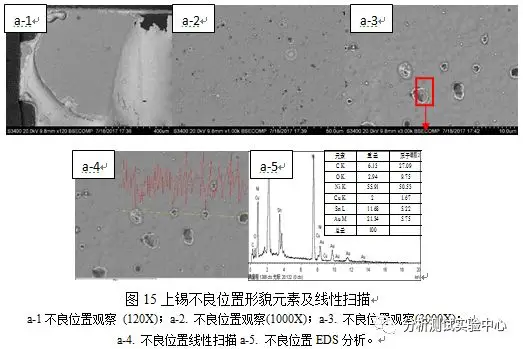
从以上分析结果可以看到,焊接不良位置发现较多孔洞。元素分析结果显示,上锡不良位置含C(碳)、O(氧)、P(磷)、Ni(镍)、Sn(锡)、Au(金)等元素,P(磷)、Ni(镍)来自于沉镍层,Au(金)来自沉金层,Sn(锡)来自焊料残留;其中Ni(镍)含量为50%,且线性扫描发现孔洞位置金厚接近零线,说明孔洞位置出现漏镍现象,存在金层对镍层保护不足而氧化的风险。
对不良板焊点进行截面微切片制作后观察,结果如图16所示:
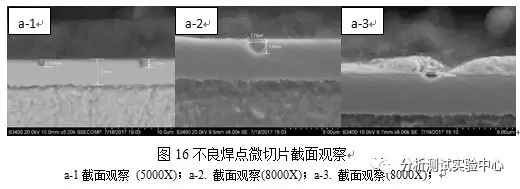
由上图可知,不良板焊盘截面微切片发现孔洞宽度在1.46μm~1.71μm之间,深度在0.45μm ~1.29μm之间,且孔洞位置出现焊接不连续的现象。由以上分析结果可知,焊点孔洞位置并非镍腐蚀,而是本身镍层存在孔洞且孔洞较大,在沉金的过程中金层无法有效沉积在孔洞内的镍层表面,导致镍离子向金层扩散氧化,引起可焊性不良现象。
2.4.2 金面划伤
以下分享一例金面划伤导致可焊性不良的案例。不良外观如下图17所示:
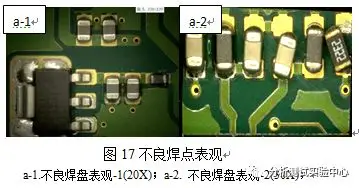
对不上锡位置金面进行形貌观察及元素分析,结果如图18所示:
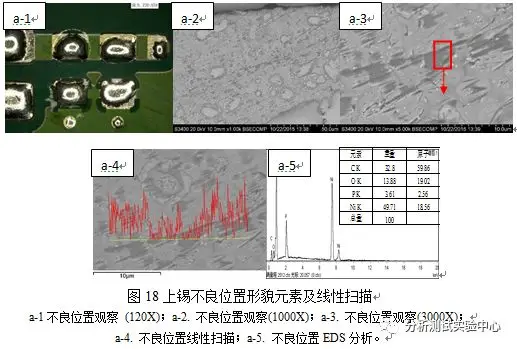
如上图所示,对上锡不良的板面进行形貌观察及元素分析,发现上锡不良位置存在密集的划伤,划伤位置存在严重露镍状况,且元素结果显示C、O含量偏高。
为进一步验证不良板可焊性问题是由于焊盘划伤处镀层保护不足所引起的,现对不良板分别采用异丙醇清洗和稀盐酸清洗后浸锡,浸锡结果显示,异丙醇清洗后浸锡可焊性未得到改善,而使用稀盐酸清洗后浸锡可焊性良好,酸洗能够有效去除板面的氧化层,说明该板可焊性不良原因是由于金层被划伤裸露在表面的镍层被氧化,引起可焊性不良。
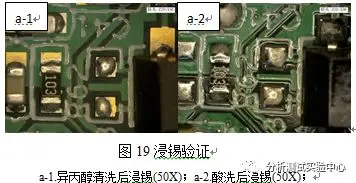
2.4.3 金面喷砂
以下分享一例金面喷砂导致可焊性不良的案例。不良外观如下图20所示:
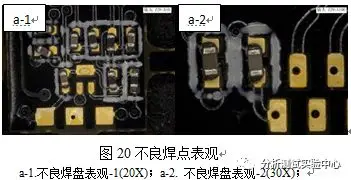
对不上锡位置金面进行形貌观察及元素分析,结果如图21所示:
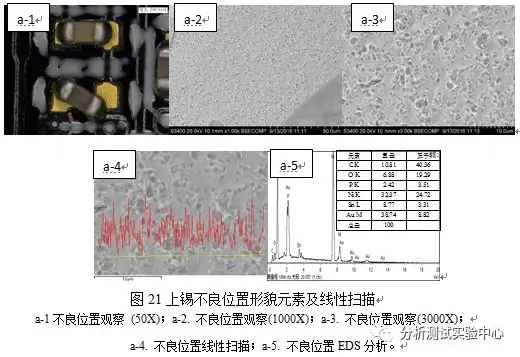
如上图所示,对PCBA上锡不良位置形貌观察及元素分析,发现上锡不良位置形貌异常,为喷砂后的金面形貌;沉金金面喷砂会导致金厚变薄,甚至破坏金层对镍层的保护导致露镍,露出的镍暴露在空气中被氧化,在焊接时会影响焊料与焊接基底镍层之间形成金属间化合物IMC层,导致可焊性不良上锡不良。元素分析未发现其它异常特征元素;线性扫描结果显示线扫描露镍。
(1)常见的化学沉镍金可焊性不良原因主要有以上案例中提到的几点:镀层厚度不足、金层表面污染、镍腐蚀、镀层损伤等;
(2)在焊接过程中,镀层最大的作用就是保护焊接面不受氧化、污染,在焊料铺展时,基底层能够与锡料快速融合,形成质量可靠的焊点。镍层作为金层和铜层之间的过渡层,起到阻挡铜和金相互扩散的作用,同时其还是焊接的基底层,所以金层偏薄或者金层出现损伤或者镍层本身存在质量问题,都将存在对镍层保护不足引起可焊性不良的风险。
[1] 李伏等.你了解沉锡吗?[J] .印制电路信息,2014,No.4:41-57
[2] 贾忠中等.无铅PCB的表面处理与选择[J].电子工艺技术,2017,38(6):364-369
[3] 邓涛等.化学沉镍金速率分析与应用[J].印制电路信息,2011,NO.12:52-2
[4] 安维等.沉金PCB焊盘不润湿问题分析方法研究[J].电子工艺技术,2018,39(39):154-178
作者简介:
崔思萍,现就职于广州兴森快捷电路科技有限公司分析测试实验中心,任失效分析助理工程师,主要从事各项物理、环境、可靠性等检测分析研究及PCB/PCBA板级失效分析技术研究。
罗定锋,现就职于广州兴森快捷电路科技有限公司分析测试实验中心,任失效分析助理工程师,主要从事各项物理、化学、环境、失效检测分析研究及PCB/PCBA板级失效分析技术研究。